brock
Major Website Supporter
MEGA KILOVOLT-MASTER
Posts: 3,459
|
Post by brock on Jan 24, 2013 0:09:32 GMT -5
I'm sure Tom will come along & make it right  As an electrician, I just wanted to try to see if you could check continuity on your contacts when they're made up. Sometimes they look closed (made up) & indeed are touching correctly but just don't have the cleanliness to carry the electricity like they should. Maybe the contacts just need a good cleaning 
|
|
Deleted
Deleted Member
Posts: 0
|
Post by Deleted on Jan 24, 2013 0:46:41 GMT -5
Skip (brbluesman) is not the first or last to be absolutely reach their last wit fiddling with the open/close contacts. For me, it is the only tough part of re-working the motors. Last one I worked on, I spent 5 hours trying to get it exactly right...and finally gave up. And I do believe that what Brock is saying is 100% true. In hindsight, I believe that at some point I had the contacts set up right but they were not clean enough to permit good consistent conductivity. It's really a fairly primitive electro mechanical set-up, so my guess is that those contacts really have to be both corrosion free and well adjusted. And while I do have a FSM (Factory Service Manual) (factory service manual) for reference, it really is not in depth enough to help a whole lot.
As a result of this thread, I have been asked a couple times if I would be willing to fix/restore other peoples motors. That was never my intent.... and frankly I don't feel absolutely confident in my work yet to do that. One that I did for myself, "tested good" off the car, but much to my dismay, failed miserably when I put it on my car. At this point I still consider myself a novice.
On the bright side...I did buy a new blasting cabinet a few months ago and have manged to find a number of cores (not for sale) for me to further experiment with...and hopefully further hone my skills. #2Thumbs# #2Thumbs#
|
|
|
Post by brbluesman on Jan 25, 2013 8:39:55 GMT -5
Tom, you made me feel much better. I was beginning to think I wasn't as handy as I thought I was. I spent at least 10-12 hours working on mine. My contacts were clean, but what I think was my problem was the adjusting of them. Also, I found that if you don't de-solder the mounting plate that the cams and switches are on, it could cause trouble. If left soldered, it's hard to line up the plate when you put it back on the gear. if you bump the contacts at all doing this, they come out of alignment. So de-soldering so that you can drop the plate on from the top, straight down, is very important. I believe this to be the cause of most of the problem I had. My only problem now is the doors are slamming when closing. I guess I'm missing rubber stops/bumpers ?
|
|
Deleted
Deleted Member
Posts: 0
|
Post by Deleted on Jan 29, 2013 11:58:12 GMT -5
Well, it has been awhile since I have done anymore headlight motor work. Decided to pull out my cores today and get started on another batch. 15 cores to do, mostly JY finds, a couple eBay purchases. Plus another 2 to re-do that were cosmetically done previously but failed to work properly. The good news is that I believe I figured out why a couple failed. Every time I do this, I learn a little more. Maybe one day I'll become an expert. In the head housing there is a small cup like bushing that stabilizes the end of the motor shaft. Usually it stays put. I think I had one or two fall out in the glass beading process...and I never realized it. The end result being a motor that would work when tested off a car, but would bind badly when put thru the rigors of a on the car test. I will now be removing these bushings prior to media blasting...so they don't get blasted out and lost. You can get them out with a pick. location of bushing in disassembled motor head  up close pics of bushing 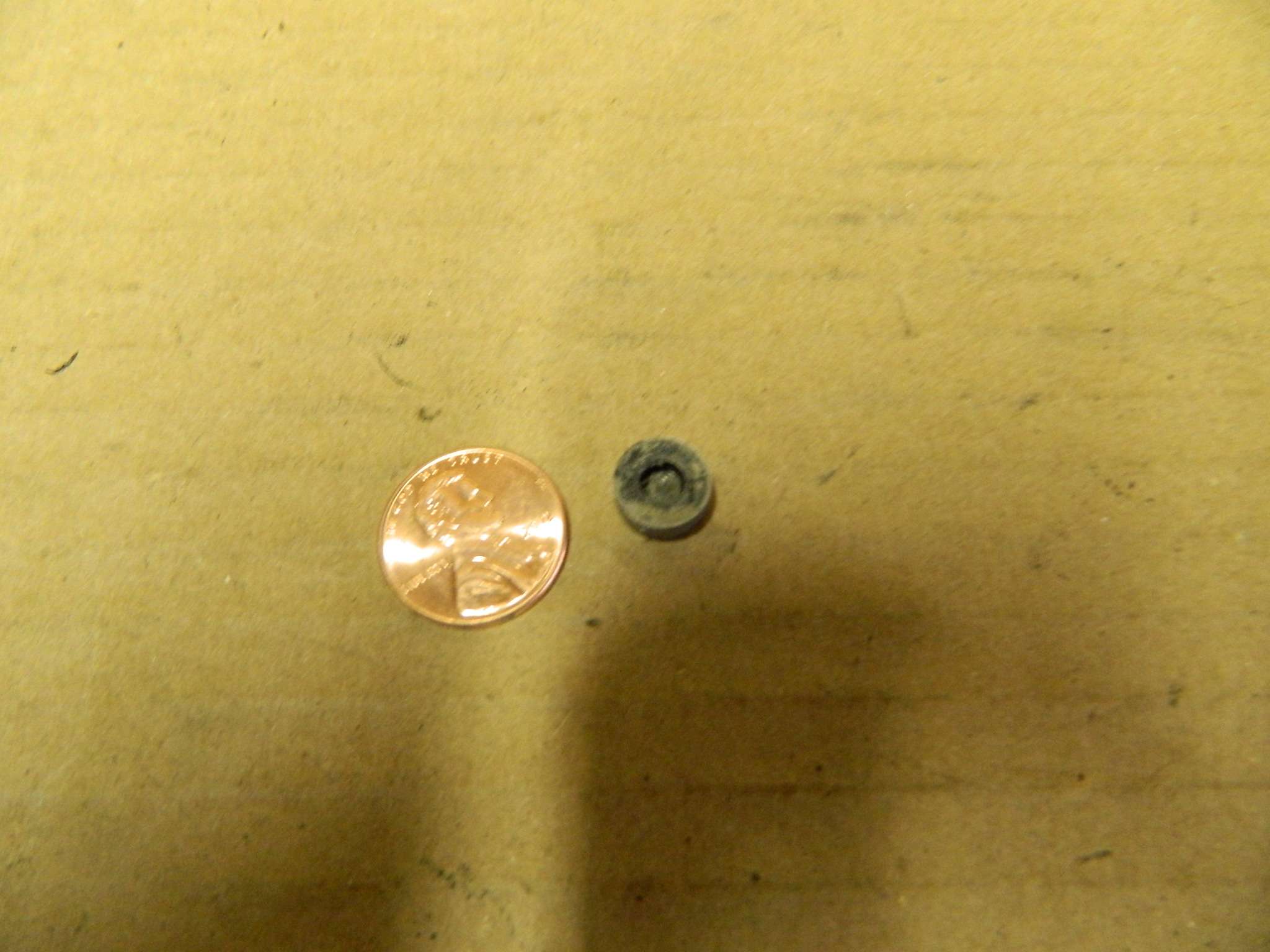
|
|
Deleted
Deleted Member
Posts: 0
|
Post by Deleted on Jan 29, 2013 20:29:55 GMT -5
|
|
Deleted
Deleted Member
Posts: 0
|
Post by Deleted on Jan 29, 2013 20:43:33 GMT -5
I tore down 17 motors today. 2 that looked to have been worked on previously were missing that bushing I mentioned earlier. Again, I had several issues with the shaft on the armature being seized to the lower bushing. I managed to work most of them out, but two pulled the bushing out of it's retainer...and proceeded to damage the brush plate. So, though I may have 22 or so housings ready to freshen up, I think I only have 16 or 17 lower sections with good brush plates. Out of the 17 motors I tore down, only 2 had re-usable thrust bearings. I think only one had a stripped gear. 2 of the motors had the shorter armatures. The difference seems to be all at the bottom where the end knob gets pressed on. On those motors, the knob was visibly closer (very close) to the housing.
|
|
Deleted
Deleted Member
Posts: 0
|
Post by Deleted on Jan 30, 2013 0:44:04 GMT -5
One other thing that I found interesting. Most of the headlight motor gears are only half moons. (approximately) 3 of the ones I have are complete 360 degree units. 2 of those have a couple square teeth, that I assume effectively work as mechanical "stops" 1 has no square teeth. (the black one) 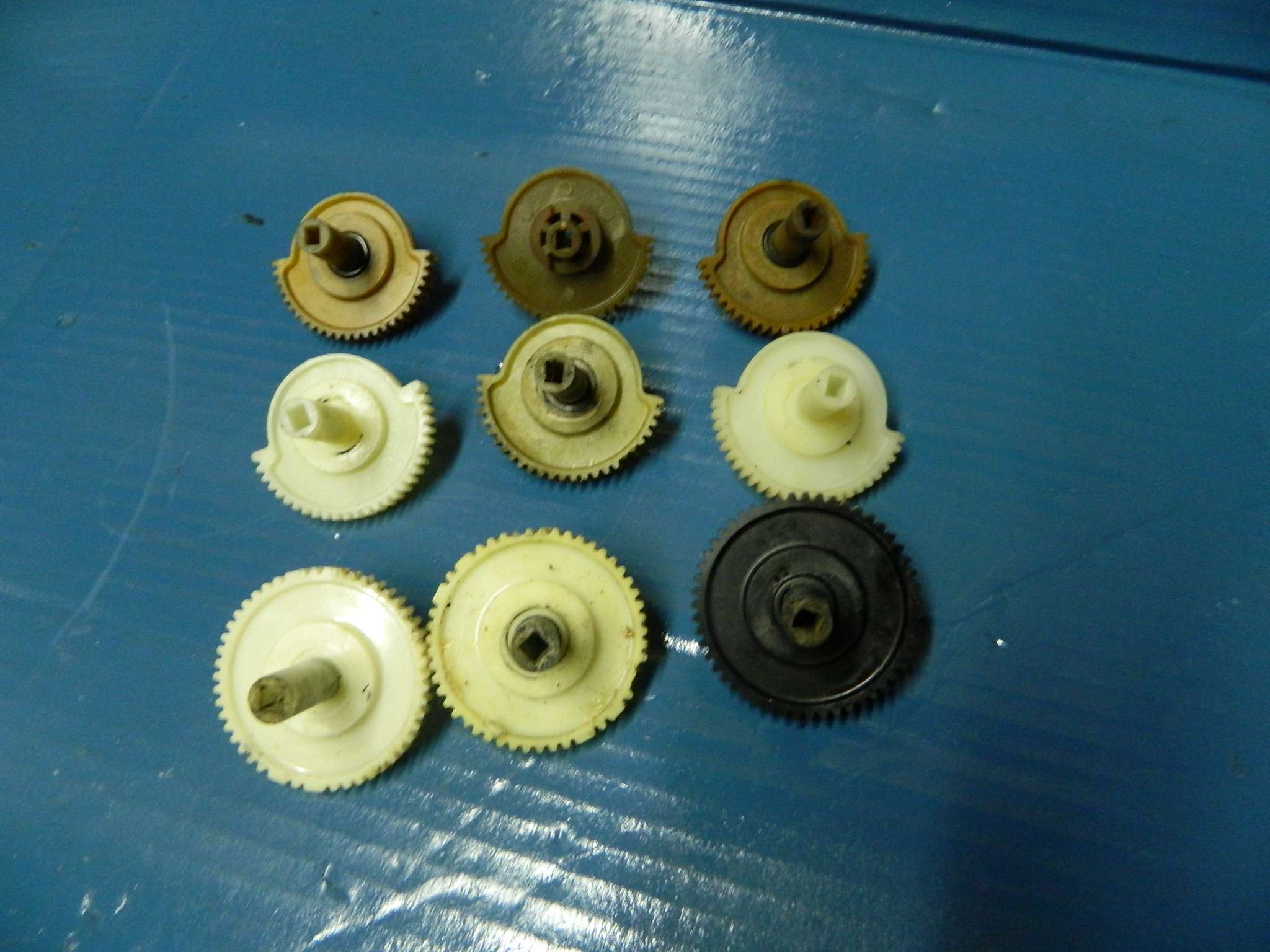 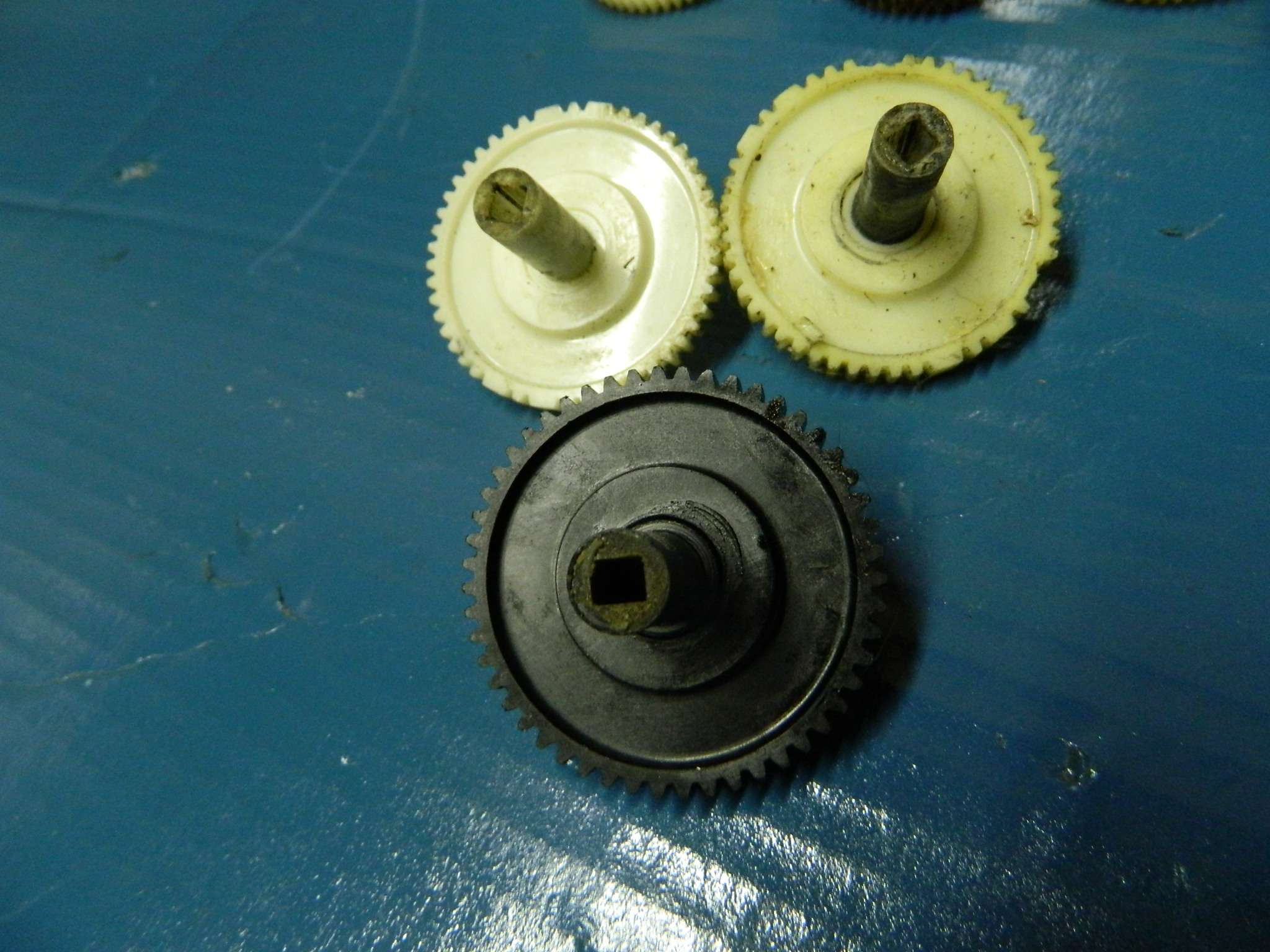
|
|
DynoDave
CO-ADMINISTRATOR
Motown Mopar-Wizard
Posts: 11,269
|
Post by DynoDave on Jan 30, 2013 6:49:00 GMT -5
Got a little glass beading to do.  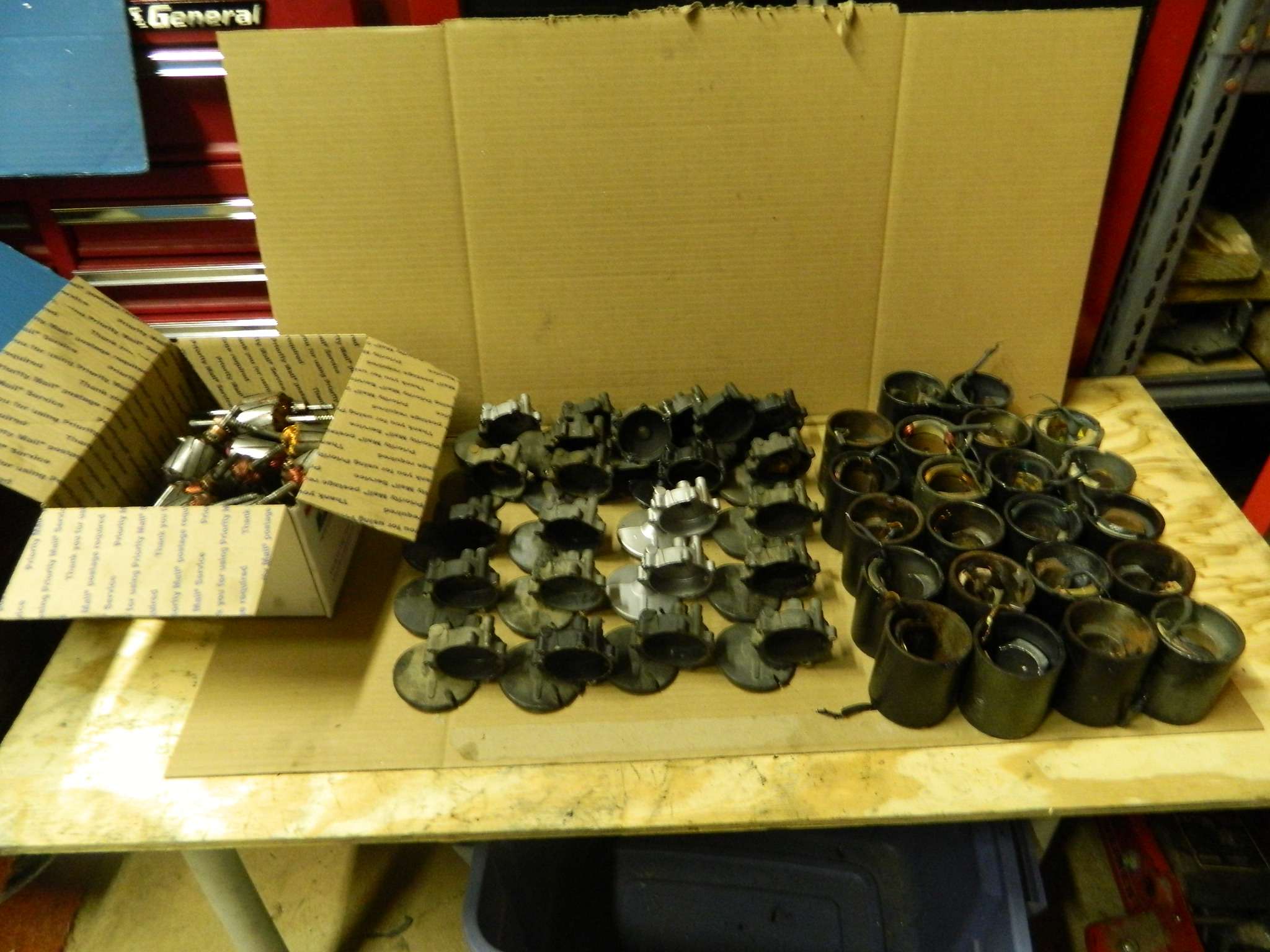 This is interesting to follow Tom. Especially all the little variations you are finding. In the photo above, I notice 2 of the housings on the left side of the table are shiny silver, while the rest are black. I "assume" they are all made the same, but the black ones are all painted, where the silver ones are not? Are those two silver ones the ones you think may have been rebuilt before?
|
|
Deleted
Deleted Member
Posts: 0
|
Post by Deleted on Jan 30, 2013 8:41:33 GMT -5
Dave, the silver ones were simply ones that I had done before. One of them had failed an on the car test, the other I had problems getting the limit switches set up right.
|
|
|
Post by MrSnicks on May 28, 2013 11:05:24 GMT -5
Any updates Tom? Let's see the shiny repaired motors after you've carefully reworked them to better-than-new condition.
Patrick
|
|